Physical vs. Computer Models in Fuel System Design
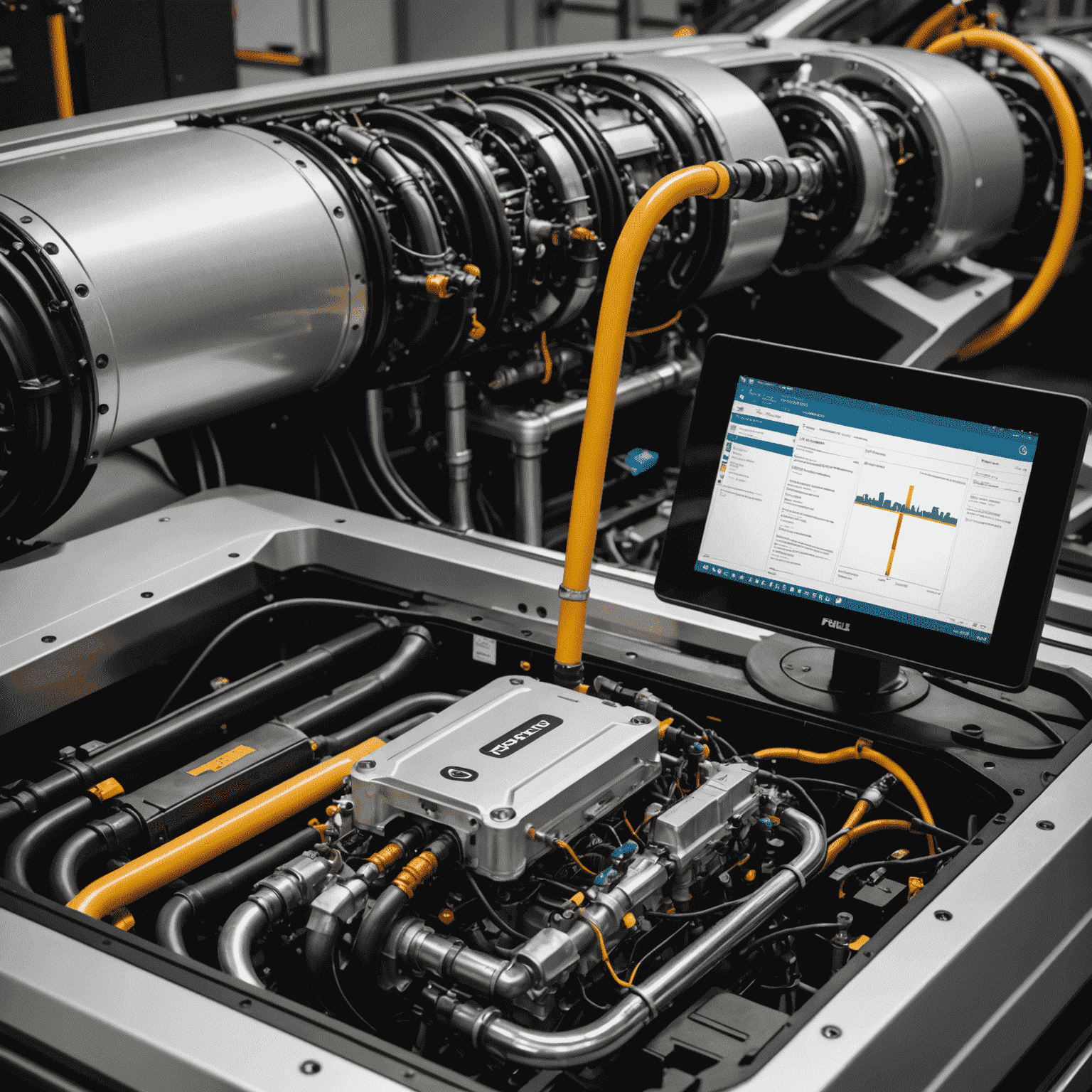
In the realm of fuel system design, engineers are faced with a crucial decision: whether to rely on physical models or computer simulations. Both approaches offer unique advantages and challenges, and understanding their pros and cons is essential for creating efficient and reliable fuel systems.
Physical Models: Tangible Insights
Physical models, also known as prototypes or mock-ups, provide a tangible representation of fuel systems. These models allow engineers to interact with the system components directly, offering several benefits:
- Tactile Understanding: Engineers can physically manipulate components, gaining a hands-on understanding of how different parts interact.
- Real-World Behavior: Physical models accurately represent fluid dynamics and mechanical interactions that might be challenging to simulate digitally.
- Immediate Feedback: Issues with fit, assembly, or basic functionality can be identified quickly during the construction process.
- Stakeholder Engagement: Non-technical stakeholders can more easily understand and provide input on physical models.
However, physical models also come with limitations:
- Cost and Time: Building physical prototypes can be expensive and time-consuming, especially for complex systems.
- Scale Limitations: It may be challenging or impossible to create full-scale models for large fuel systems.
- Modification Difficulties: Making changes to physical models often requires rebuilding, which can be resource-intensive.
Computer Models: Digital Precision
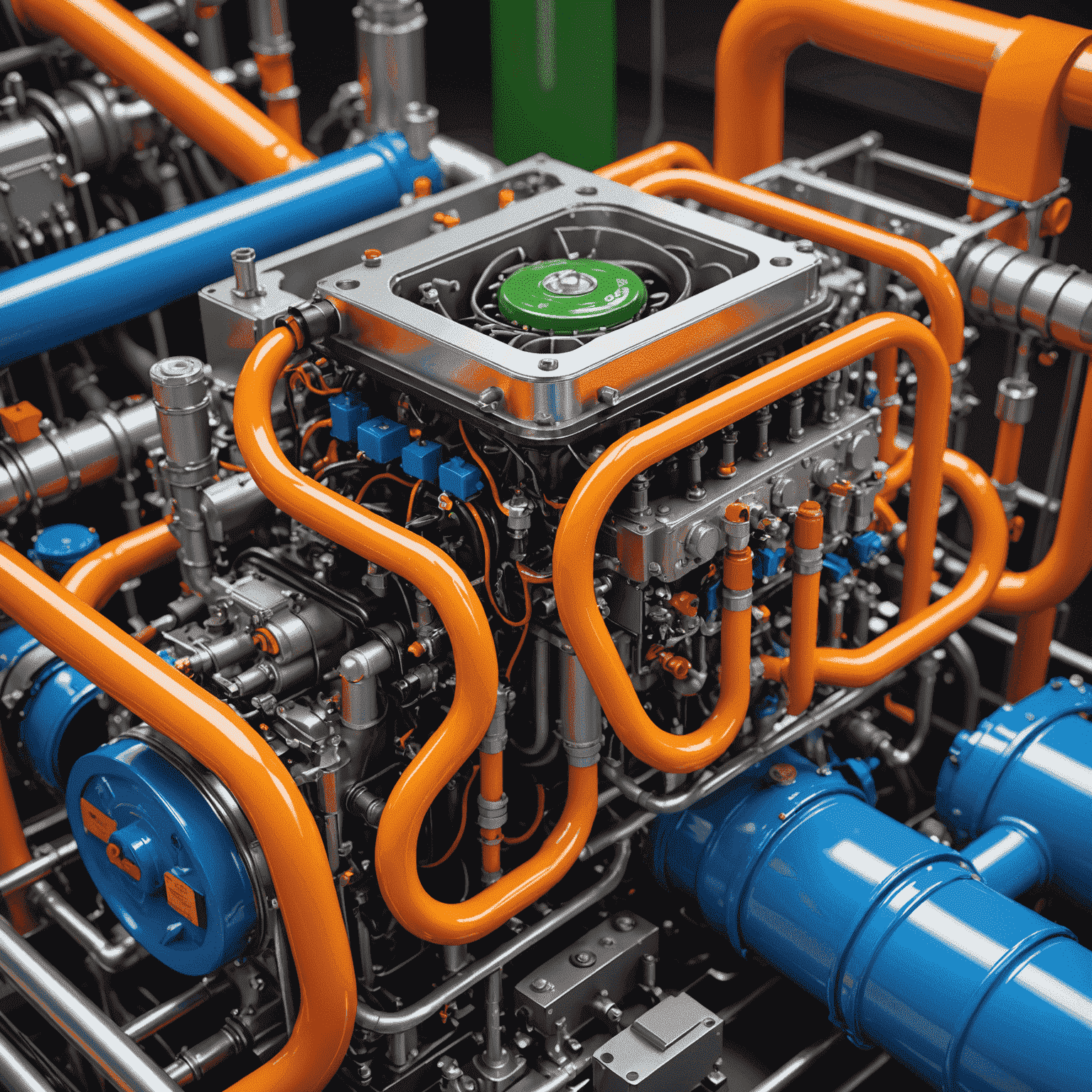
Computer models, or simulations, leverage advanced software to create virtual representations of fuel systems. These digital models offer several advantages:
- Rapid Iteration: Changes can be made quickly and easily, allowing for fast design improvements.
- Complex Analysis: Advanced simulations can model intricate phenomena like fluid dynamics, heat transfer, and structural stress.
- Cost-Effective: Once the initial software investment is made, running multiple simulations is relatively inexpensive.
- Scalability: Computer models can easily represent systems of any size, from small components to entire fuel networks.
However, computer models also have their drawbacks:
- Abstraction: The lack of physical interaction can make it harder to intuitively understand certain aspects of the system.
- Accuracy Limitations: The quality of the simulation depends on the accuracy of the input data and the sophistication of the modeling software.
- Computational Resources: Complex simulations may require significant computing power and specialized hardware.
Finding the Right Balance
In practice, many fuel system designers opt for a hybrid approach, leveraging the strengths of both physical and computer models. This balanced strategy might involve:
- Using computer simulations for initial design and optimization
- Building physical prototypes of critical components for validation
- Refining the computer model based on physical testing results
- Iterating between physical and digital models as the design progresses
This combined approach allows designers to benefit from the rapid iteration and complex analysis capabilities of computer models while still gaining the tactile insights and real-world validation offered by physical prototypes.
Conclusion
Both physical and computer models play crucial roles in fuel system design. The choice between them—or the decision to use both in tandem—depends on factors such as project scope, budget, timeline, and the specific challenges of the system being designed. By understanding the strengths and limitations of each approach, engineers can make informed decisions to create more efficient, reliable, and innovative fuel systems.