Real-world Applications of Fuel System Simulations
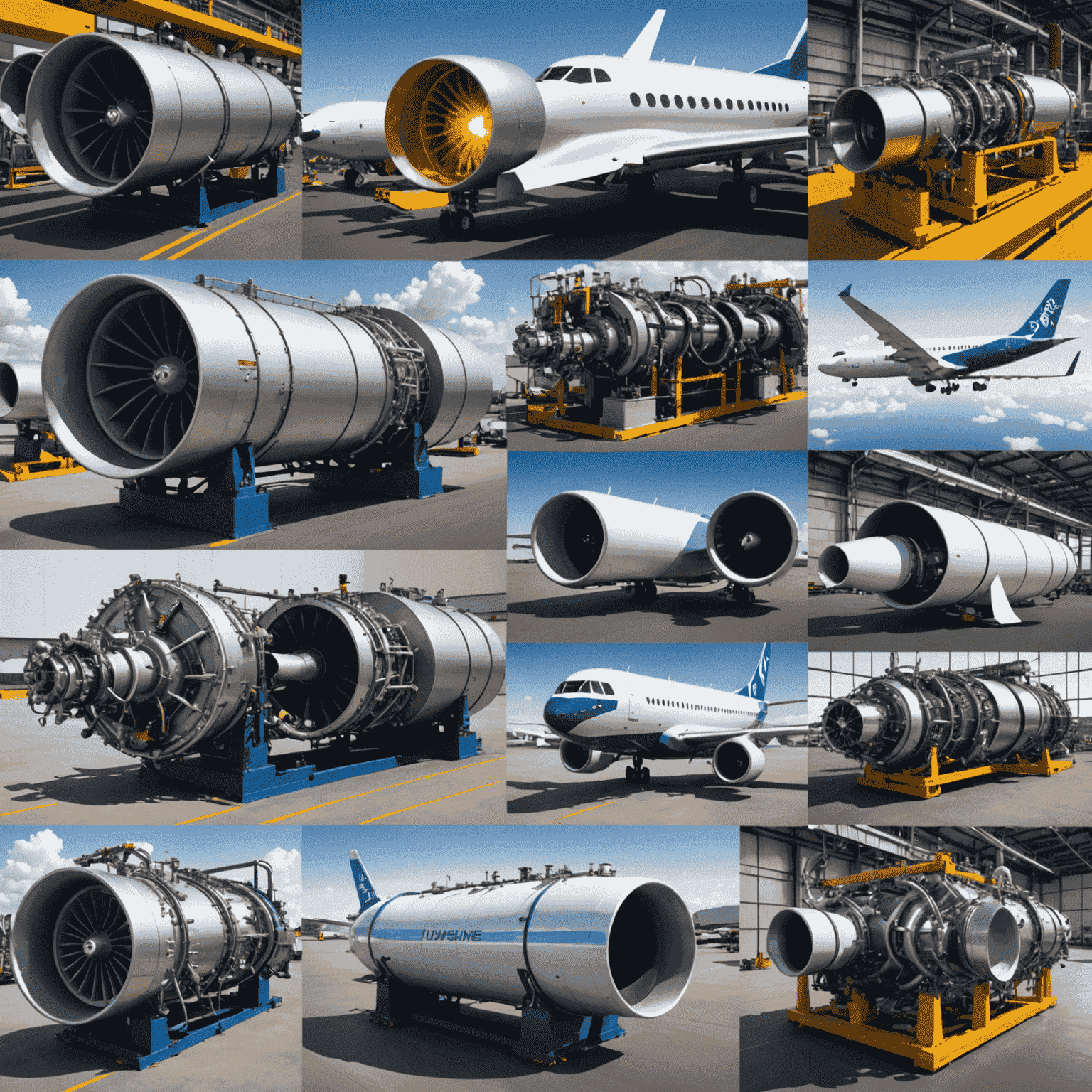
Fuel system simulations have revolutionized how industries approach efficiency and performance. Let's explore some compelling case studies that demonstrate the power of these advanced modeling techniques.
Automotive Industry: Enhancing Fuel Efficiency
In the automotive sector, a leading manufacturer utilized fuel system simulations to optimize their engine design. By creating a detailed computer model of the fuel injection system, engineers were able to:
- Reduce fuel consumption by 8% in city driving conditions
- Improve engine response time by 12%
- Decrease harmful emissions by 15%
These improvements were achieved without the need for costly physical prototypes, saving both time and resources in the development process.
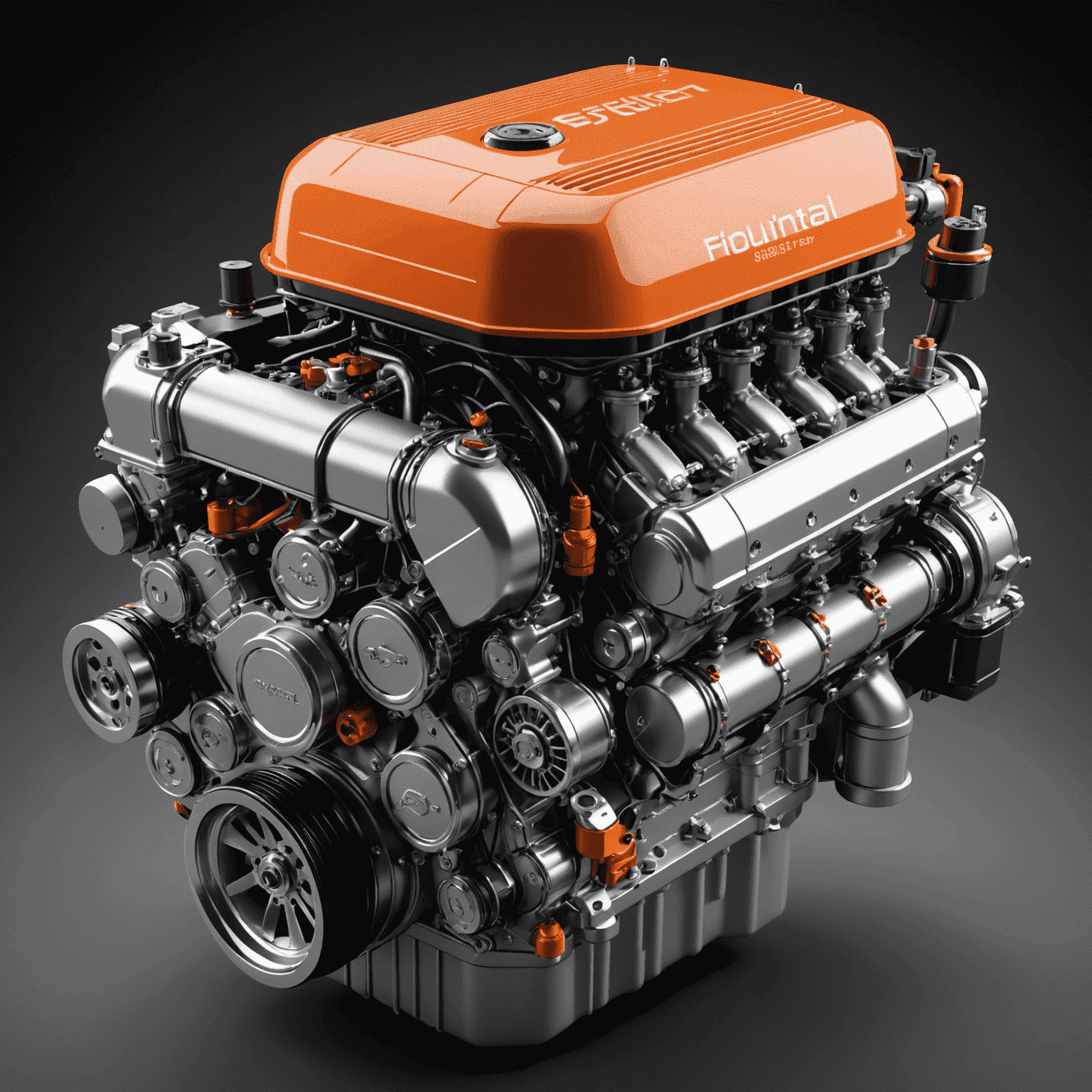
Aerospace: Optimizing Aircraft Fuel Management
A major aircraft manufacturer employed advanced fuel system simulations to address challenges in long-haul flights. The simulations allowed engineers to:
- Redesign fuel tank geometry, increasing capacity by 5% without changing the aircraft's external dimensions
- Improve fuel pump efficiency, reducing power consumption by 7%
- Enhance fuel distribution systems, leading to better weight balance and a 3% increase in range
These advancements significantly improved the aircraft's performance and competitiveness in the market.
Marine Industry: Enhancing Ship Fuel Systems
In the shipping industry, fuel system simulations have been instrumental in adapting to new environmental regulations. A container ship operator used simulations to:
- Design a dual-fuel system capable of running on both traditional marine diesel and liquefied natural gas (LNG)
- Optimize fuel switching procedures, reducing transition times by 30%
- Improve overall fuel efficiency by 10%, leading to significant cost savings and reduced emissions
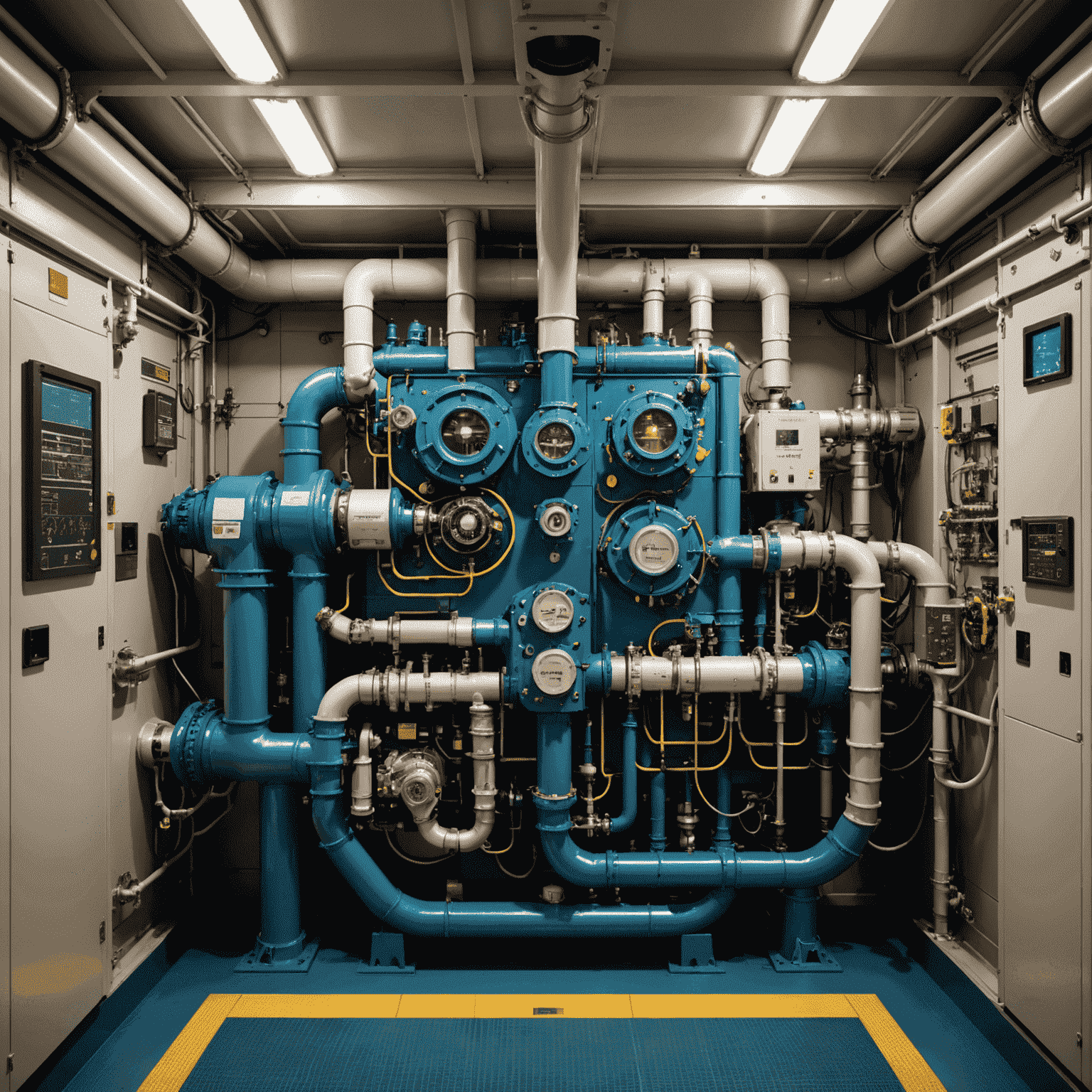
Power Generation: Improving Gas Turbine Performance
A power plant operator utilized fuel system simulations to enhance their gas turbine operations:
- Redesigned fuel nozzles increased combustion efficiency by 6%
- Optimized fuel flow control reduced startup times by 15%
- Improved fuel distribution led to a 4% increase in overall power output
These improvements resulted in significant cost savings and increased electricity production capacity.
Racing Industry: Pushing the Limits of Performance
In the high-stakes world of motorsports, a Formula 1 team leveraged fuel system simulations to gain a competitive edge:
- Optimized fuel delivery systems improved engine power output by 2.5%
- Redesigned fuel tank baffles reduced fuel slosh, enhancing car stability in corners
- Improved fuel consumption models allowed for more aggressive race strategies
These marginal gains, made possible through precise simulations, translated into improved lap times and race results.
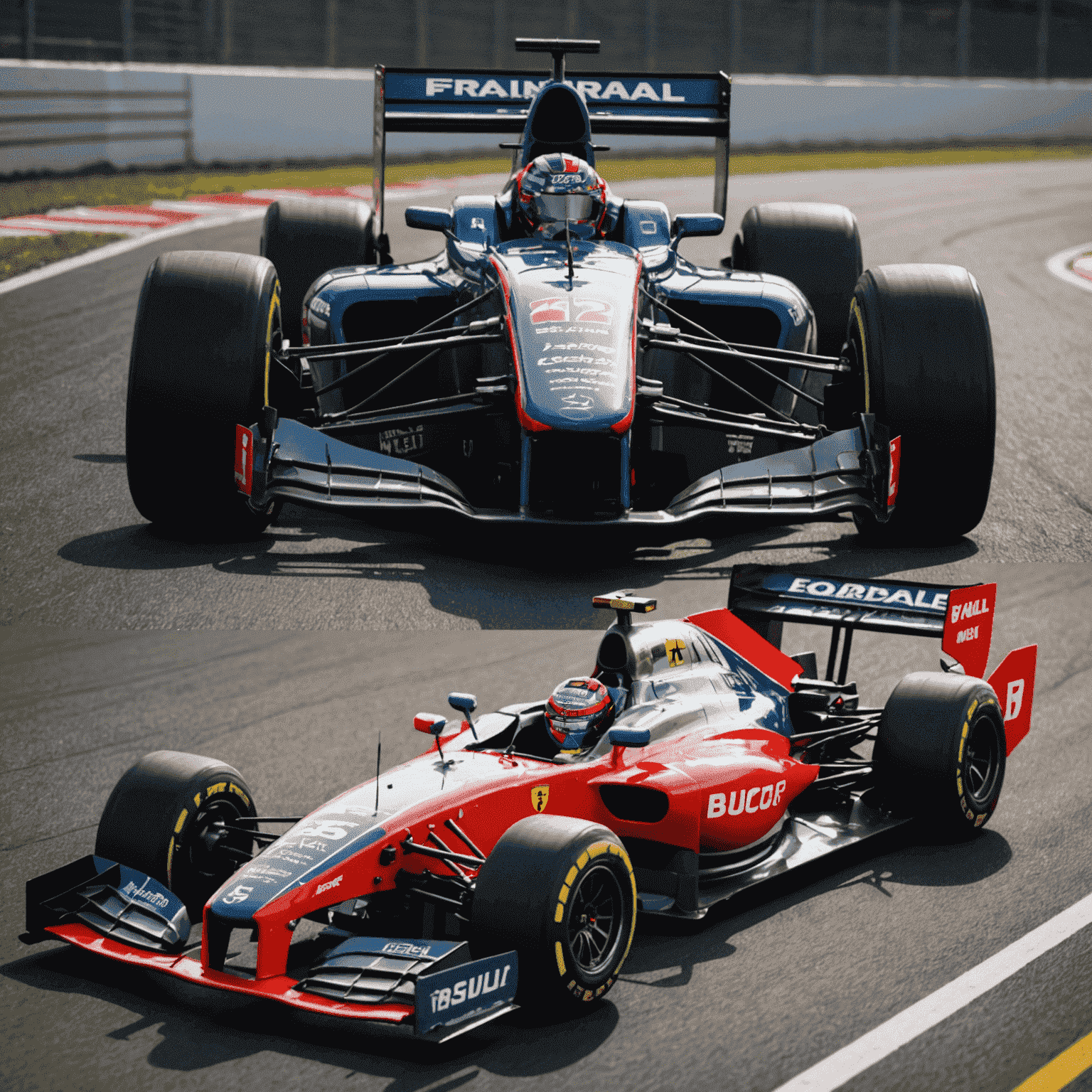
Conclusion: The Power of Fuel System Simulations
These case studies clearly demonstrate the wide-ranging benefits of fuel system simulations across various industries. By creating accurate computer and physical models, engineers can:
- Significantly improve efficiency and performance
- Reduce development time and costs
- Enhance environmental sustainability
- Drive innovation in fuel system design
As simulation technologies continue to advance, we can expect even more groundbreaking improvements in fuel systems across all sectors, further pushing the boundaries of what's possible in energy efficiency and performance.